Biomass, RDF and sludge milling
Biomass milling is one of the more energy-consuming processes. Its task is to bring biomass to the required particle sizes. It depends on the quality of fragmentation that the energy expenditure on biomass pelleting, the wear of dies and rollers as well as the operation of the technological line.
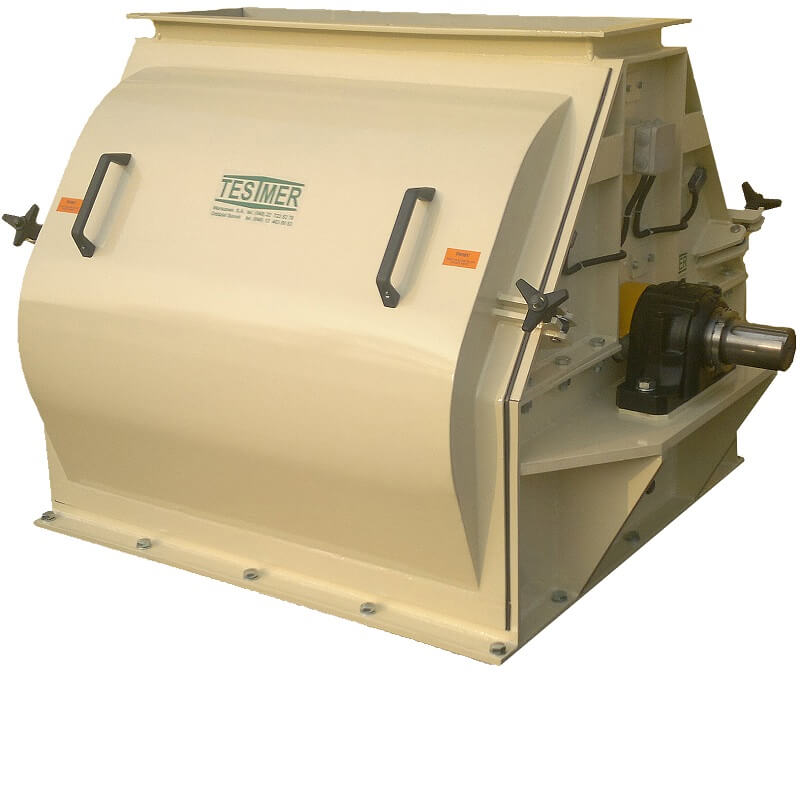
Comminution of Biomass
Testmer designs and supplies grinding lines based on the following devices:
- horizontal hammer mill RB-H – as the main grinding machine,
- DS screw feeders. – ensuring proper feeding of biomass,
- WMS magnetic separators, other separators, dust reduction device – to eliminate unwanted metal waste in the raw material and to ensure raw material purity and reduce dust formation
The grinding lines are each time adapted to the needs of customers in terms of performance, required fragmentation, adapted to the raw material used, acceptable dimensions etc.
Hammer Mills for Biomass RDF or Sludge
RB-H horizontal hammer mill have been designed for comminution biomass. The mill can be equipped with an electric motor with a capacity of 37 to 160 kW. Motors are adapted to work with the inverter.
Pneumatic or electric opening interlock used as safety equipment. The elements used make the machine a trouble-free and safe device.
Hammer mills have following advantages:
- energy saving
- simple and compact construction,
- silent work,
- easy assembly and replacement of screws
- reliable, durable construction.
Examples of output on straw.
Type | Power [kW] | Output [t/h] * |
---|---|---|
RB-H75 | 75 | up to 2,2 |
RB-H90 | 90 | up to 3.0 |
RB-H110 | 110 | up to 3.5 |
Example of output on soft wood
Type | Power [kW] | Output [t/h] * |
---|---|---|
RB-H37 | 37 | up to 1.0 |
RB-H75 | 75 | up to 1.7 |
RB-H132 | 132 | up to 3.5 |
* – Capacity is presented roughly. It may vary depending on the density of the material, humidity and its mechanical parameters.
Feeders
The feeders offered in the grinding lines ensure even dosing of the raw material to the hammer mill. The capacity of the feeder is adjusted by a frequency converter. The feeder has a large inspection door that allows cleaning the inside of the feeder and a air filter.
The dimensions of the feeder are adapted to the size and output of the hammer mills they will work with.
Magnet separators
The task of the magnets is to separate ferromagnetic bodies from biomass. They are particularly suitable as a protection in comminution and pelleting lines. They are made of stainless steel.
The capacity of the magnets is determined by its diameter.
Basic parameters of the magnetic separators for biomass are presented below:
Type | Diameter [mm] | Capacity [t/h] * |
---|---|---|
WMS-150 | 150 | up to 1.0 |
WMS-200 | 200 | up to 1.5 |
WMS-250 | 250 | up to 2.8 |
WMS-300 | 300 | up to 5.0 |
WMS-350 | 350 | up to 6.5 |
* – The capacity is approximate for biomass with a density of 0.2 t / m3 and may vary depending on the density of the material, humidity and its mechanical parameters.
Separators and anti dust equipment
The TESTMER offer includes the following devices used in comminution lines:
- stone or coarse sand separators,
- patron dust collectors with self cleaning, which ensure effective dust reduction,
- special tanks under the hammer mills to improve the mills capacity
Tanks, input hoppers
TESTMER offers comprehensive biomass processing solutions including:
- flat tanks for raw material equipped with a movable floor,
- vertical tanks with mechanical agitator or pressure aeration system,
- receiving baskets with dimensions adapted to the size of the loading means.
- mamy mamy others.
We invite you to familiarize yourself with the entire TESTMER offer.
Gallery
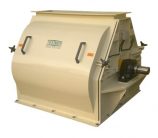
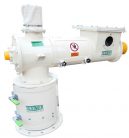
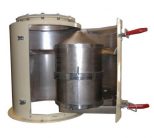

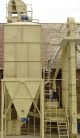
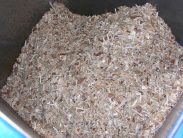
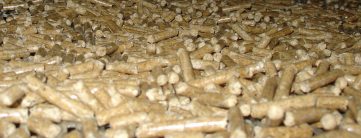
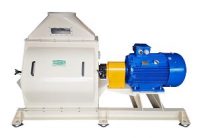
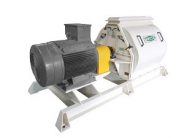
TESTMER - professional solutions for the feed production market
TESTMER WARSZAWA S.A. is the market leader in the production of technological lines for feed production in Poland. From 1991 we installed over 100 lines in Poland, Belarus, Ukraine, Russia, Italy and the Czech Republic.
The basic machine used in the feed production line is a pellet press. TESTMER started production of pelleting presses in 1991 and since then expanded its offer to include all machines related to the feed production process.
We offer warranty and post-warranty service for the feed production equipment purchased from us. Spare parts needed for the proper operation of the devices are produced by our specialized crew in our factory.
cooperation with dozens of
clients





